There is no denying that pipeline establishment demands an in-depth focus on the various steps. The same holds for repairs. Among the endless methods to implement, drying and dewatering pipes remain significant moves. But what’s the significance of these processes? Let’s find out the reasons in this article.
Amidst knowing the importance of dewatering pipelines, one should delve deeper into the multiple options of pipeline drying. That’s the only way to address your underlying queries and bring hope for clarity. As you gain momentum while reading this post, every piece of information appears in front of your eyes. Let’s go!
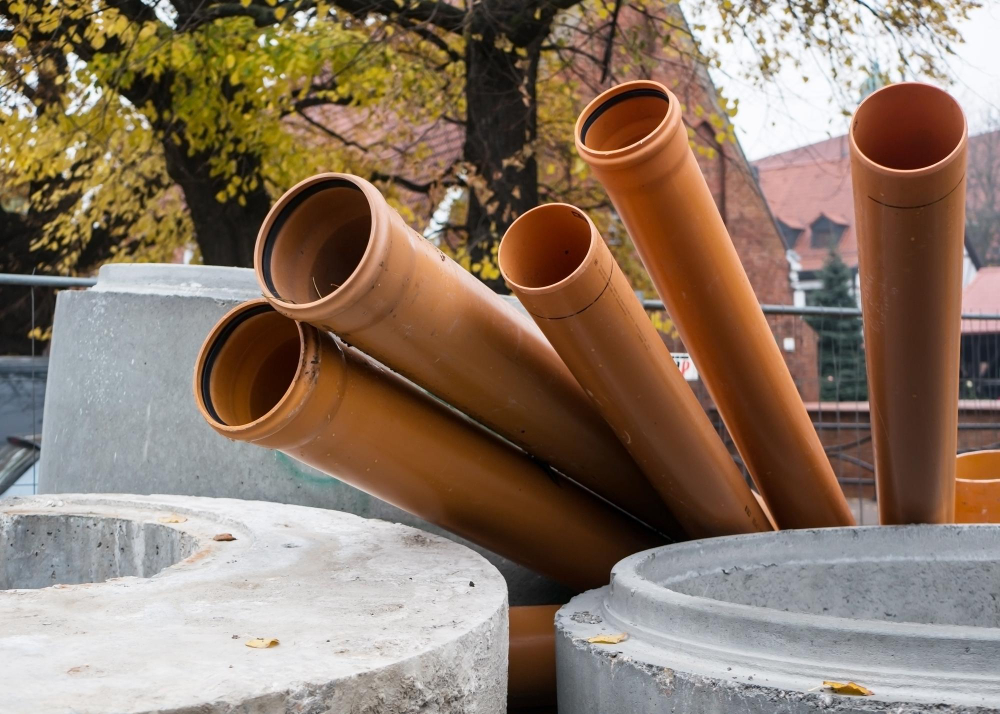
The Valuable Stuff Regarding Dewatering Pipes and Pipeline Drying
Here is the first thing to note: operators gain pipeline safety and suitability help with the support of hydrostatic testing companies. The process, however, leaves a drawback.
The residual water remains stuck within the channels, causing two severe complications:
- Accelerated Rate of Corrosion.
- Fluid Purity Alteration.
The Path to Efficiency: As operators realize and utilize the pipeline drying process, they minimize the chances of these errors and sustain efficient pipeline functioning.
Familiarize Yourself with the Pipeline Drying Methods
Dewatering pipes and pipeline drying require specific processes for implementation. Let’s discuss each crucial option one at a time:
The Hot Air Method: This process resembles the nitrogen pipeline dewatering path. However, the difference arises due to the use of industrial air compressors to supply heated air. What can you expect? As heated air accesses wet pipelines, water vapor formation accelerates.
This evaporated moisture undergoes conduction to the pipe’s opposite end at the exit port’s location.
The Monitoring Device: Transmitters and hygrometers are necessary for examining hot air pipeline tests. These devices can automatically and effectively monitor outlet and inlet air dewpoint variations.
Use of Nitrogen for Pipeline Drying: Another efficient method for dewatering pipelines is utilizing gaseous nitrogen. Here are the factors that make this element suitable for pipeline drying:
- It remains non-reactive.
- Nitrogen’s static nature accounts for its stability.
The process involves the introduction of nitrogen gas at one end of the pipe. Its chemical nature allows the various impurities and residual water to exit the pipeline from the other end.
When Does the Process Meet Completion? Fulfillment arrives as the outlet gas and feed gas dewpoint attains a variation of 10 degrees Fahrenheit.
Other Methods in a Nutshell
Let’s take an overview of other pipeline drying methods.
Noticing Vacuum Drying: This procedure involves sealing the pipelines from both ends and attaching a single port to a vacuum device to eliminate residual water and air.
Observing Chilled Air Drying: Dry and chilled air can significantly remove moisture from the selected pipelines. Industrial chillers take credit for establishing sub-zero temperatures and letting the water out.
MEG Drying Process: In this case, moisture goes away due to exploiting mono ethylene glycol’s hygroscopic properties.
Putting an End to the Piping Requirements
Are you looking for quality steel pipes for a specific purpose? Let BigFoot Pipe & Piling extend its helping hands to you. We believe in satisfying clients by providing customization benefits and
- Used
- New
- Surplus Pipes
Allow the quality work to make noise and view our inventory for further information.