“Quality welding is the backbone of sturdy connections in steel projects,” said an anonymous welding expert. Employing the correct welding method for optimal results is essential for joining steel components.
In this article, we delve into three standard methods for welding steel and explore their advantages. Within the realm of structural steel fabrication, various welding techniques hold their significance. TIG welding or gas tungsten arc welding empowers welders with exceptional control, while resistance or spot welding emphasizes efficiency and MIG welding or gas metal arc welding showcases remarkable versatility. Each method finds its purpose and importance in the diverse landscape of steel fabrication. By understanding these methods, you can make an informed decision that ensures robust and reliable welds, guaranteeing the integrity and longevity of your steel projects.
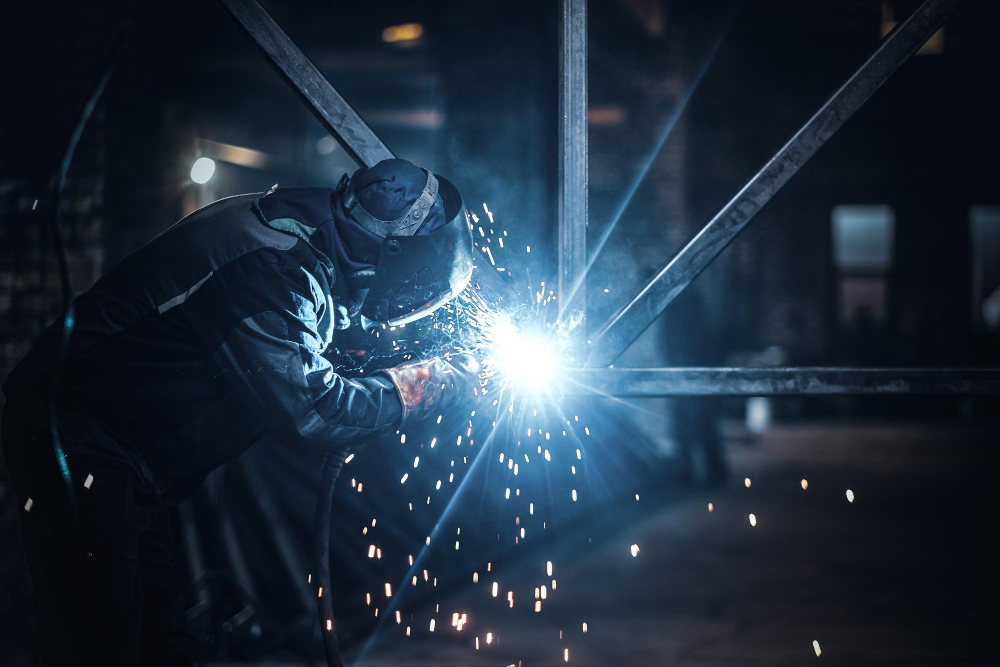
TIG Welding: Sparking Precision And Steel Beauty
TIG welding, or gas tungsten arc welding, is a precise and versatile method commonly used in structural steel fabrication. This technique employs a tungsten electrode to create an electric arc, which generates the heat necessary to melt the base metal and a filler rod if required. TIG welding offers exceptional control over the welding process, allowing welders to produce high-quality and visually appealing welds with minimal spatter. This method is well-suited for thinner gauge materials, intricate designs and applications requiring precise welds, such as aerospace and automotive industries.
Resistance Or Spot Welding: The Quick Fixers Of Steel Connections
Resistance or spot welding is famous for joining steel components in structural fabrication projects. This technique involves applying pressure and electrical current to the workpieces, causing localized heating and subsequent fusion at the contact points. Resistance welding is highly efficient and produces strong welds without additional filler material. Sheet metal fabrication, automotive assembly and appliance manufacturing commonly employ this method. Spot welding enables rapid production and is favored when speed and cost-effectiveness are essential.
MIG Welding: Metal Magic – Arc Welding With A Twist
MIG welding, or gas metal arc welding, is a versatile and widely adopted structural steel fabrication method. This process employs a consumable wire electrode continuously fed into the weld pool and shielding gas to protect the weld from atmospheric contamination. MIG welding offers excellent productivity and can be used on various thicknesses of steel, making it suitable for both light and heavy fabrication projects. Adjusting the welding parameters allows for versatility in achieving different joint designs and weld characteristics. Consequently, MIG welding finds applications in industries ranging from construction to shipbuilding.
Battle Of The Welders: Which Structural Steel Fabrication Method Reigns Supreme?
Determining the best steel welding method depends on several factors, including the specific requirements of the fabrication project. TIG welding excels in producing precise and visually appealing welds, making it ideal for applications that prioritize aesthetics and require intricate designs. Resistance or spot welding, on the other hand, offers high-speed production and is suitable for joining thin sheet metals in mass-production environments. MIG welding balances versatility and productivity, making it a popular choice for various fabrication projects.
Embrace The Legendary Strength Of Bigfoot Pipe & Piling For Your Steel Fabrication Needs!
Are you ready to elevate your steel fabrication projects to new heights? Choose Bigfoot Pipe & Piling as your trusted partner! Our team of experts specializes in delivering top-notch structural steel fabrication services that surpass expectations.
- With our cutting-edge technology, exceptional craftsmanship and unwavering commitment to quality, we’ll help you build a solid foundation for success.
- Take advantage of the opportunity to work with industry leaders.