Navigating the maze of pipe fitting standards can seem like a complex task, yet it’s crucial for the seamless operation of many sectors. From the flow of water to the movement of oil, these rules ensure everything works as it should. They dictate the safety, quality, and efficiency of many systems we rely on every day. As we explore these standards, it’s essential to recognize the role of trusted industrial pipe suppliers. Their expertise and quality materials are key to meeting these standards, ensuring projects not only start off on the right foot but also stand the test of time.
Standards Vs. Codes- Understanding The Distinction
In pipe fitting, “standards” and “codes” often get used interchangeably, yet they hold distinct meanings. Standards outline specifications and guidelines for the design, material, performance, and manufacture of pipe fittings. They ensure uniformity and reliability across applications. Codes, on the other hand, are sets of rules that govern the installation and inspection of pipe systems to enhance safety and compliance. They often incorporate various standards to form a comprehensive regulatory framework.
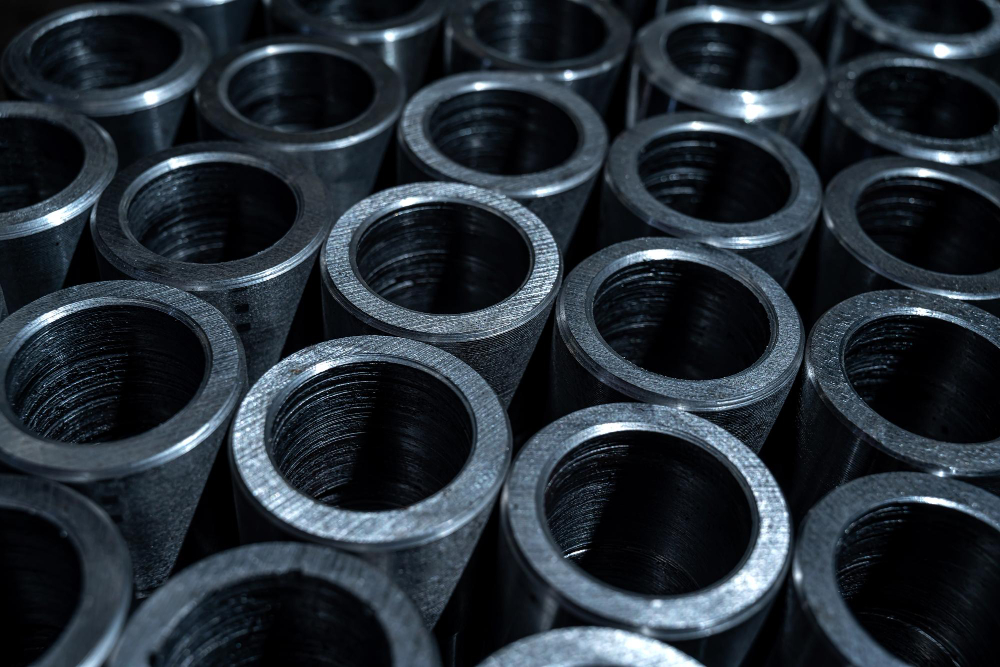
Key Factors Influencing Pipe Fitting Standards
Several crucial elements dictate the development and application of pipe fitting standards. These include:
- Pressure-Temperature Ratings: The resilience of fittings against varying pressures and temperatures.
- Size & Design: Ensuring compatibility and efficiency in system layout.
- Coatings: Protection against corrosion and wear.
- Materials: Suitability for specific applications (e.g., stainless steel for corrosion resistance).
- Marking: Clear identification of specifications.
- End Connections & Dimensions: Guaranteeing a secure and precise fit.
- Tolerances: Allowing for manufacturing variations.
- Threading & Pattern Taper: Ensuring leak-proof connections.
Pipe Fitting Standards From Renowned Bodies
American National Standards Institute (ANSI)
ANSI, a cornerstone in the standardization landscape, fosters the development of American national standards. It introduces “schedule numbers,” categorizing wall thickness to match various pressure demands, a critical consideration for industrial pipe suppliers ensuring product compliance.
American Society for Mechanical Engineers (ASME)
Ensuring the efficiency and safety of industrial piping systems demands strict adherence to established standards. The American Society of Mechanical Engineers (ASME) and the American National Standards Institute (ANSI) have set forth a series of standards that serve as the foundation for the design, manufacturing, and application of pipe fittings. Below, we explore these standards in detail, highlighting their significance and application in the industry.
- The ASME/ANSI B16.1 – 1998 standard delineates requirements for cast iron flanges and related fittings, highlighting their use based on specific pressure and temperature considerations. It plays a vital role in assuring the strength and dependability of systems incorporating cast iron parts.
- The ASME/ANSI B16.3 – 1998 standard sets forth criteria for malleable iron threaded fittings, ensuring these components are capable of withstanding the pressures and temperatures assigned to them, thus offering a dependable option for a variety of industrial settings.
- In line with B16.3, the ASME/ANSI B16.4 – 1998 standard is dedicated to the specifics of cast iron threaded fittings, providing detailed requirements for their effective and safe incorporation into piping networks.
- Expert industrial pipe suppliers recommended ASME/ANSI B16.5 – 1996 standard presents an exhaustive set of specifications for pipe flanges and flanged fittings, covering dimensions, tolerances, and materials suitable for various pressure and temperature scenarios to ensure safe and compatible use in diverse conditions.
- Targeting robust connections, the ASME/ANSI B16.11 – 2001 standard addresses forged steel fittings, including those for socket welding and threading, outlining best practices for their application in scenarios requiring high pressure.
- The ASME/ANSI B16.14 – 1991 standard establishes the essential specifications for ferrous pipe plugs, bushings, and locknuts with pipe threads, aiming to secure these fittings properly and maintain the integrity of the piping structure.
- For cast bronze threaded fittings, the ASME/ANSI B16.15 – 1985 (R1994) standard specifies the characteristics required for their longevity and ability to resist corrosion, ensuring they fulfill the demands for durability.
- According to experienced industrial pipe suppliers, the ASME/ANSI B16.25 – 1997 standard offers guidance on designing buttwelding ends for piping elements, advocating for a connection approach that is both secure and efficient.
- Focusing on orifice flanges, the ASME/ANSI B16.36 – 1996 standard elaborates on the dimensions, pressure ratings, and additional essential details needed for their role in flow rate measurement within piping systems.
Industrial pipe suppliers and engineers must familiarize themselves with these standards to ensure that the components they select and use meet the rigorous demands of their applications. Compliance with ASME/ANSI standards not only ensures the safety and reliability of piping systems but also contributes to their long-term performance and efficiency.
ASTM International
ASTM stands out for its comprehensive standards covering a wide array of materials and applications, crucial for industrial pipe suppliers to meet diverse industry needs. Its guidelines span from high-temperature service to special applications like fire protection, setting a benchmark for quality and reliability.
Military Standards (AN)
The AN standard, born from military needs, emphasizes precision in measurement, highlighting the importance of external diameter for fitting sizes. This unique approach underscores the adaptability and precision required in pipe fitting standards, ensuring compatibility and performance across various applications.
The Role Of Industrial Pipe Suppliers In Upholding Standards
Industrial pipe suppliers play a pivotal role in the successful implementation of pipe fitting standards. By offering products that meet these rigorous guidelines, they ensure the integrity, safety, and efficiency of piping systems across industries. Their expertise and commitment to quality help clients navigate the complexities of standards and codes, making them indispensable partners in any construction or maintenance project.
Commitment To Excellence
At Bigfoot Pipe and Piling, understanding and adhering to pipe fitting standards is more than just about compliance for us. It’s about ensuring the safety, efficiency, and longevity of piping systems. As industrial pipe suppliers, we are dedicated to keeping ourselves and our clients informed about these standards. This dedication is key to the success of your projects and the safety of your operations. Whether you’re an engineer, contractor, or supplier, we believe in working together to ensure every project meets these critical standards. Our expertise and commitment make us a trusted partner in your endeavors.