Unfurling the mystery of the building and construction industry, we unravel an indispensable component – the humble sheet pile. Often overlooked yet undeniably essential, this ‘unsung hero’ plays a crucial role in maintaining the structural integrity of our world’s edifices. From skyscraping towers to monumental bridges, the influence of sheet piles is ubiquitous. This blog aims to shed light on this remarkable innovation, taking you on an enlightening journey through the world of sheet piles. We delve deep into their intriguing definitions, the varied forms they assume and their remarkable installation processes, courtesy of the insights from leading sheet pile manufacturers.
The Intriguing Definition Of Steel Sheet Piles
Steel sheet piles are robust, interlocking steel sheets that form a continuous barrier in the ground, creating a robust wall for retaining soil or water. They are a stalwart defense against potential ground movements or shifts that could jeopardize the structural integrity of a building.
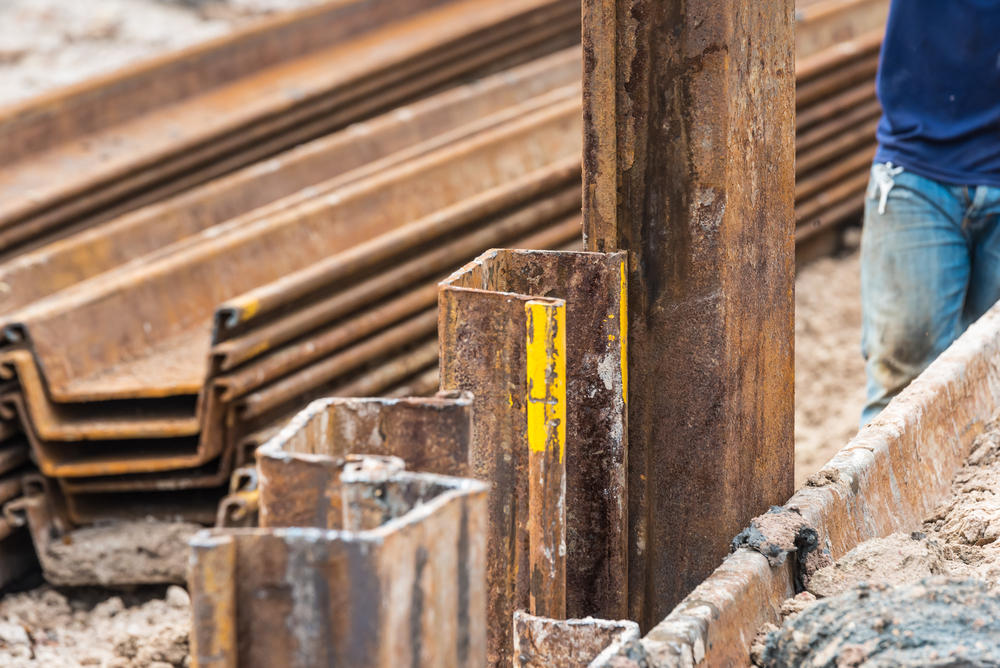
Exploring The Different Forms Of Sheet Piles
Sheet piles take on multiple forms, each with unique features and applications.
Interlocking System
- The interlocking system is one of the most widely-used forms of sheet piles due to its flexibility and adaptability.
- These sheet piles have a locking mechanism along their edges, which allows them to be connected seamlessly, forming a continuous, impenetrable wall.
- This system is particularly advantageous when constructing retaining walls that need to curve or when the wall needs to fit into a specific shape or size.
- These interlocked sheet piles provide excellent structural support and water and soil pressure resistance, making them ideal for a variety of construction projects.
Box Pile System
- The box pile system connects two or more sheet piles to form a box-shaped cross-section.
- This design increases strength and stability, particularly for heavy load-bearing structures. Marine construction often uses the box pile system, such as quay walls, where the construction needs to withstand significant lateral and vertical loads.
- These interconnected piles form a robust structure, offering superior load distribution and structural efficiency.
Straight Web Sheet Pile System
- Unlike the traditional Z or U-shaped piles, straight web sheet piles have a straight, flat design. These piles suit environments where retaining water is crucial, such as cofferdams, dikes and barriers.
- Their straight design allows them to resist high water pressure and form circular cells effectively, typically used for enclosing construction sites in the water or building structures like breakwaters.
Composite Pile System
- Composite sheet piles combine the best attributes of steel and vinyl or concrete materials to create a product that offers strength, durability and corrosion resistance.
- These composite piles offer a long service life and can be a cost-effective alternative in projects where corrosion resistance is paramount, like marine or industrial environments.
- Furthermore, they can be manufactured in various shapes and sizes to meet specific project requirements.
Describing The Whole Installation Thing
The installation of sheet piles is a fascinating process, often carried out in these sequential steps:
Planning
- The initial phase of sheet pile installation involves thoroughly evaluating the construction site, including factors such as soil type, groundwater levels and potential obstacles (like underground utilities).
- This stage also involves studying the project requirements, like the anticipated load on the wall, the desired wall height and the expected environmental conditions.
- The results of this assessment help in determining the most appropriate type and size of sheet piles, the optimal installation method and any additional support measures that may be necessary.
- This stage often involves collaboration between engineers, geologists and sheet pile manufacturers to ensure the best possible outcomes.
Pile Driving
Once the planning phase is complete, the actual installation begins. This process, known as pile driving, involves using specialized equipment to push or hammer the sheet piles into the ground.
There are two common types of hammers used for this purpose: vibratory hammers and impact hammers.
- Vibratory hammers use rapid vibrations to reduce the friction between the pile and the soil, allowing the pile to drive effortlessly into the ground. This fast method causes less noise and vibration, making it suitable for urban areas.
- On the other hand, impact hammers use a heavy weight to deliver blows to the top of the pile, driving it into the ground. This method is best for more complex soil conditions or deeper penetration needs.
Interlocking
As the sheet piles penetrate the ground, their interlocking edges are connected to form a continuous, impenetrable wall. This process involves careful alignment of the piles to ensure a seamless connection and a sturdy, robust wall.
The interlocking mechanism provides the wall with structural integrity and helps to resist the lateral pressures from soil or water.
Cut-Off And Tie-Back Installation
- Once the sheet piles have been installed and interlocked, they may be cut to the desired height to align with the construction design. Using a cutting torch or a hydraulic cutter helps execute the process.
- In some cases, particularly for taller walls or in poor soil conditions, additional support is necessary to ensure the stability of the sheet pile wall.
- These rods or cables are drilled into the ground at an angle and then connected to the wall, providing additional resistance to lateral forces.
Buying From Reputable Sheet Pile Manufacturers: Ensure An Impressive Project Outcome
Investing in products from reputable sheet pile manufacturers can be a game-changer for any construction project:
- Quality Assurance: “Quality’s no game of chance, it’s a manufacturer’s firm stance.” High-grade materials guarantee durability and longevity.
- Technical Support: Expert advice can streamline installation and maintenance.
- Cost-Effective: Superior products reduce the need for frequent replacements or repairs.
- Customization: Reputable manufacturers offer a range of options to suit unique project requirements.
Bigfoot: Let Us Build A Resilient Future Together
With Bigfoot Pipe & Piling, you will receive products manufactured to the highest standards, tailored advice from our seasoned experts and a partnership built on trust, quality and mutual growth. Together, we can create strong structures against time and nature, forging a legacy of enduring infrastructures.
So, leap toward a successful construction project with trustworthy sheet pile manufacturers like us. Get in touch today – let’s shape a world that’s not just built to last but designed to impress!